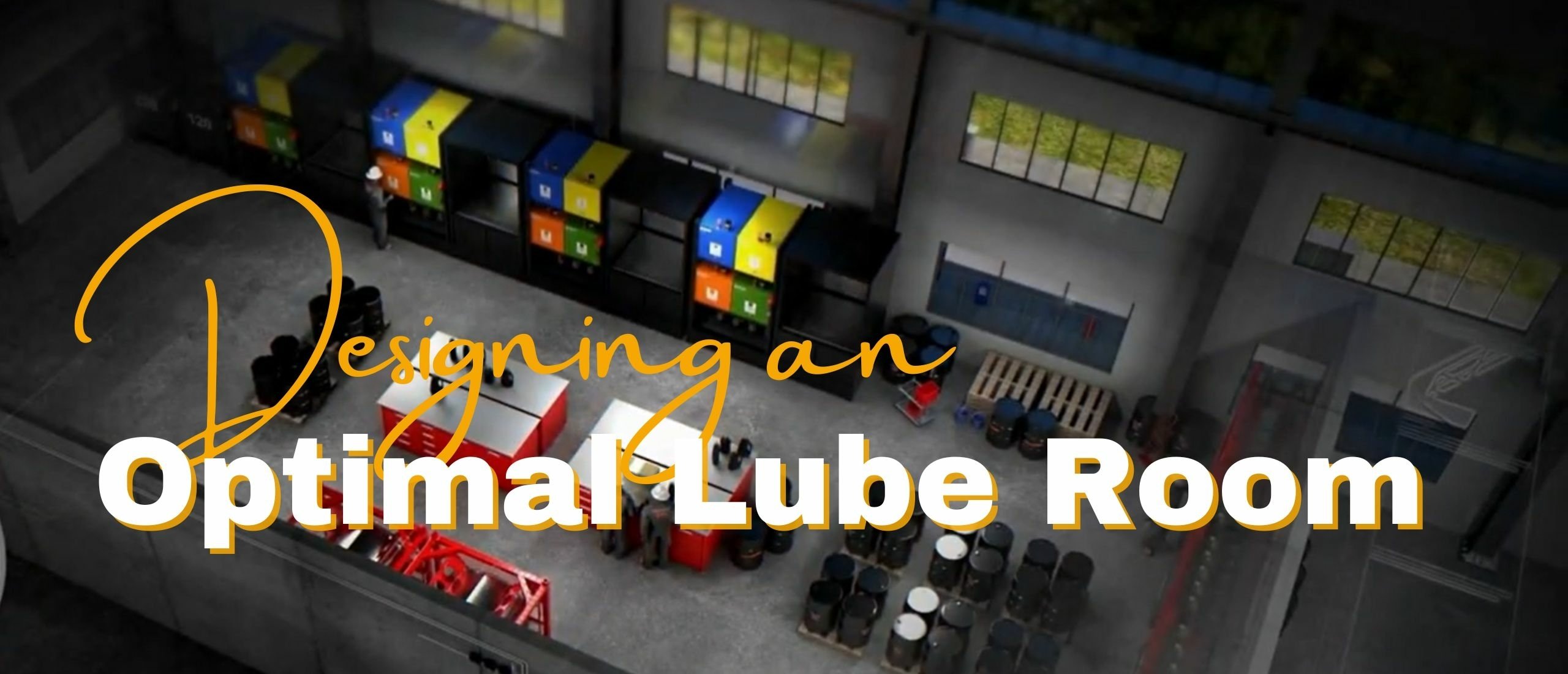
Lube Rooms
Designing an Optimal Lube Room
05/14/2024
Achieving peak plant and machine reliability hinges on Lubrication Reliability™ (LR), guided by the principles of the 6 Rights in Lubrication. Central to this is the design of a high-functioning Lube Room, optimizing storage, dispensing, and protection of lubricants. This guide delves into essential steps and criteria for crafting a LR-compliant space, essential for maintaining superior lubrication standards.
Unlocking the Power of Lubrication Reliability™ Through Strategic Design and Implementation"
Pre-Design Preparation:
- Streamline lubricant types and brands.
- Establish a Plant Lubrication Identification Standard ( PLIS ).
- Test new lubricant supplies for ISO 4406 cleanliness.
- Ensure compliance with local Safety & Environmental regulations.
Selection Criteria:
Assess location options:
- existing room vs. new construction,
- indoor vs. outdoor,
- centralized vs. decentralized storage.
Consider packaging preferences:
- existing drums/containers vs. new tanks/reservoirs for bulk storage.
Minimum Recommendations:
New Lubricant Supply:
- Prioritize storage in a dry, cool, and clean environment.
- Implement FIFO strategy and PLIS labeling.
- Segregate from dispensing areas.
- Regularly remove expired lubricants based on storage conditions.
Lubricants in Use Storage:
- Opt for smallest packaging based on consumption.
- Ensure new oils meet ISO 4406 cleanliness standards.
- Employ closed circuit storage systems.
- Utilize dedicated equipment per lubricant, with non-drip Quick Connects.
- Protect from air with Desiccant Breathers.
- Install filtration systems for new oil transfer and circulation.
Lubricants in Use Dispensing:
- Use professional dispensing tools like OilSafe cans
- Dispensers should be closable to environment and 100% sealable
- Dispensers should be colour coded and lube identified ( PLIS )
- Dispensers should be translucent to see lubricant content / level
OilSafe 3L translucent can
- Dispensers should be selected in accordance with the application and lubricant type
- Dispensers should be kept clean inside & outside at all times
- Dispensers should be stored in closed cabinets or racks with retention shelves
Closed Cabinet
- Dispensers should be kept closed ( spout twisted ) at all times when not in use.
Twisted spout
Lube Room Minimal Features:
- Dedicated lube storage & dispensing equipment ( always one equipment per lube )
- Select a clean room with light coloured walls ( white/gray )
- Sufficient lighting ( LED tubes ) and needed power plugs
- Install lube storage ( drums/tanks/reservoirs ) only on proper retention equipment.
- Use as a rule-of-thumb 110% retention capacity ( can vary with local regulations ). All type of retention pallets or bunds are acceptable (steel-plastic). Care should be taken to avoid cheap light weight plastic. Drain valves are useful, not necessary.
- Mobile Containers Solutions (like Lubristation LCU) can be equipped with full retention flooring. The floor can be made of galvanized steel grid (preferred) or plastic grid . A combination of steel checkered plate to accommodate tanks or drums and galvanized grid for the free walking section is ideal.
- Mobile units in open air should be isolated ( steel wall + PU foam ) in order to keep the inside temperature stable and protect from extreme sun and freezing temperatures.
- Mobile Container solutions can be equipped with air conditioning and/or heating.
- All storage designs should be equipped with proper ventilation, minimal natural air flow or powered by electrical fans.
- All storage tanks ( steel, plastic, stainless steel ) or drums/jerry cans (steel or plastic) should be sealed off from air. This means the suction tube hose combination needs to be fixed and sealed on the drum or tank.
- Extra equipment should include MSDS folders, wipe material, absorbents (pads, rolls, ..).
- Closed cabinets with retention shelves used for small lubrication equipment like grease pumps, grease cartridges, spare parts. Open racks for storage of OilSafe cans and similar.
- Grease in bulk should be stored in dedicated grease pump systems ( GreaseStations ) . These stations should be equipped with Heavy duty grease pneumatic grease pump, follower plate protecting grease inside the drum and cover with correct dimensions. These Stations can be used to fill manual grease pumps with risk of contamination or can be mounted on trolleys to grease machines in site.
- Filter carts for dedicated use on machinery or for bulk transfer of new oils can also be stalled on retention equipment ( spill pallets /spill floor ). Filter carts also need to add PLIS.
By adhering to these guidelines, you can create a Lube Room that serves as the cornerstone of superior lubrication practices, enhancing equipment reliability and performance.
Contact us for more info on Lube Rooms