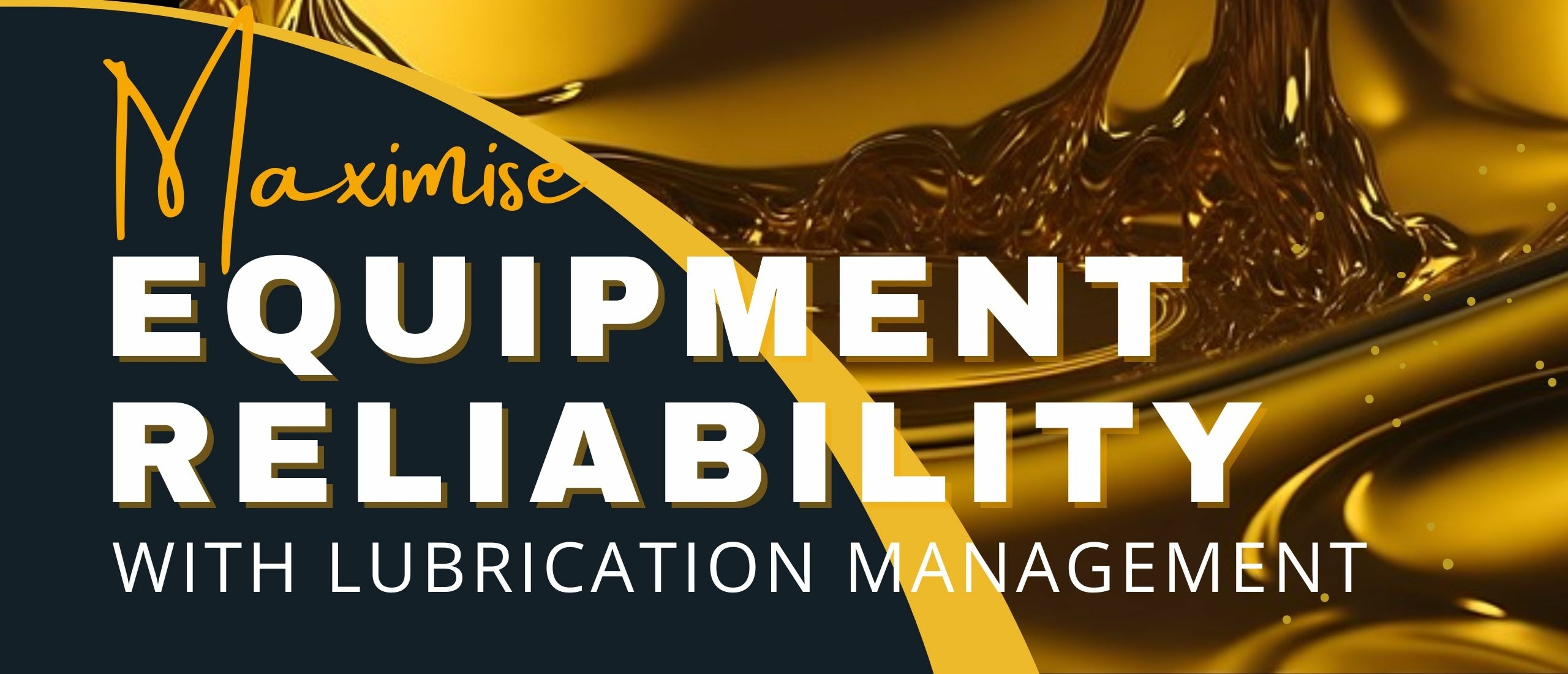
Maximise Equipment Reliability with Lubrication Management
Unveiling the Potential of Lubrication Reliability.
In today's competitive landscape, companies are constantly seeking ways to bolster their bottom line. Across industries, the strategic focus has shifted towards enhancing reliability, which translates to prolonged equipment lifespan, fewer breakdowns, and minimized maintenance needs.
Yet, amidst this pursuit, one often overlooked cornerstone of reliability reigns supreme: Lubrication Management. At its core, this entails preserving the thin film of lubricant that shields metal surfaces from wear and tear, thereby extending the operational life of machinery.
The Impact of a Robust Lubrication Strategy
Why a robust lubrication strategy matters:
- Enhances equipment reliability.
- Reduces maintenance expenses.
- Drives direct improvements in corporate profits.
While the concept may seem simple, the impact is profound. Delve into the realm of Lubrication Reliability, and you'll uncover a wealth of opportunities to optimize operational and financial outcomes.
Bearing Failures: The Costly Consequences of Lubrication Neglect
The statistics are staggering: over 60% of bearing failures can be traced back to lubrication issues. Bearings, often referred to as the beating heart of machinery, play a crucial role in ensuring smooth operation. However, when lubrication is inadequate, wear and tear become inevitable, leading to costly breakdowns and disruptions in production.
Picture this scenario:
A manufacturing plant grinds to a halt due to a bearing failure. Production schedules are derailed, maintenance teams scramble to diagnose the issue, and the financial implications begin to mount. What's often overlooked is that many of these breakdowns could have been prevented with proper lubrication management.
Achieving optimal lubrication goes beyond simply applying grease or oil. It's a multifaceted process influenced by a myriad of factors, each demanding careful consideration. Lubricant degradation, contamination, replenishment efficacy, and compatibility all come into play, shaping the effectiveness of the lubrication regimen.
Lubrication Film Thickness
What’s so important about the Lubrication Film Thickness?
Lubrication is a machine’s method of protecting its joints and ensuring that the machine as a whole is in good working order. The lubrication film creates a barrier between the softer material of the bearings and the other parts of the machine. This helps defend the bearings against the excessive wear and tear that can dramatically reduce their useful life.
Contamination, in particular, emerges as a pervasive threat to equipment longevity. Dust, dirt, water, and other contaminants infiltrate lubricants, compromising their ability to maintain the necessary film thickness. Left unchecked, this contamination accelerates wear and exacerbates the risk of bearing failures.
The dirty path of contamination
Organisations that are at Best Practice levels in managing their lubrication activities understand that oil can be contaminated in the process from when it is received at the store, and when it is running in the machine.
Below are some examples of how the lubricant can become contaminated along the way.
Fortunately, research conducted by experts like Dr. MacPhearson sheds light on the importance of clean lubricants in extending machine life. Studies examining the correlation between filter ratings and bearing fatigue reaffirm the critical role that cleanliness plays in equipment reliability.
In essence, addressing lubrication challenges head-on is essential for safeguarding equipment and preserving operational efficiency. By implementing robust lubrication management practices, companies can mitigate the risk of bearing failures, reduce maintenance costs, and ensure uninterrupted production.
ISO 4406 - the cleanliness code explained
ISO 4406 is the reporting standard for fluid cleanliness. According to this standard, a code number is assigned to particle count values derived at three different micron levels: greater than 4 microns, greater than 6 microns and greater than 14 microns.
Crafting a Successful Lubrication Reliability Strategy
So, how can companies cultivate a robust lubrication reliability strategy?
Investment is key. Procuring quality products, refining processes, and nurturing a knowledgeable lubrication workforce are essential steps. While this may necessitate upfront expenditure, the returns are undeniable:
- Reduced spending on bearings.
- Lower maintenance costs.
- Increased production efficiency.
In essence, the return on investment for a well-executed lubrication strategy speaks for itself—a prudent decision for any forward-thinking company.
Conclusion: Embracing Lubrication Excellence
In conclusion, the journey towards enhanced reliability begins with acknowledging the pivotal role of lubrication management. By embracing this fundamental aspect, companies can not only safeguard their equipment but also pave the way for sustainable business success.