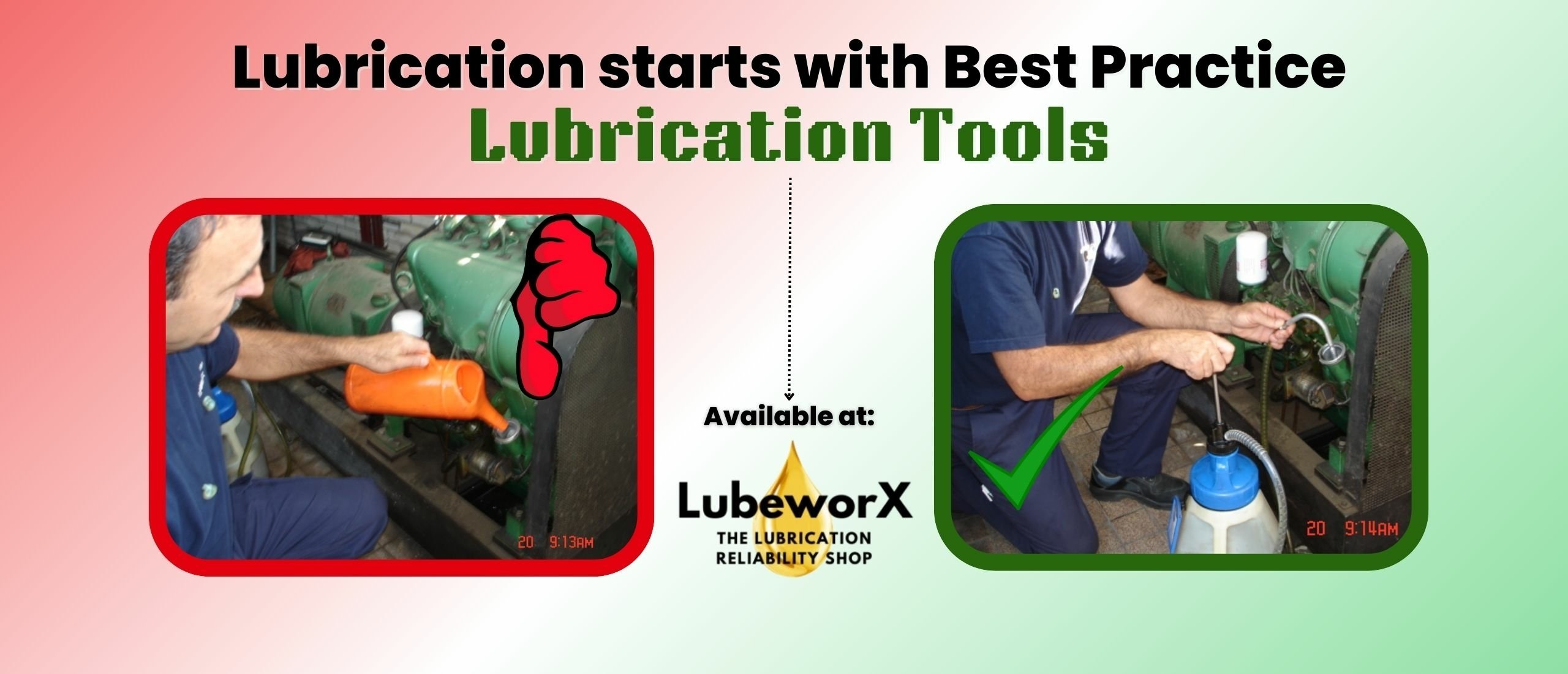
Maximizing Lubrication Reliability
Introduction to Lubrication Reliability
In industrial environments, machinery and equipment undergo constant stress, which makes reliable lubrication crucial to keep operations smooth and prevent costly downtime. Proper lubrication ensures the parts run efficiently, extends their lifespan, and minimizes wear and tear. However, achieving consistent lubrication reliability isn’t always straightforward. From contamination to using the wrong tools, minor oversights can lead to significant consequences, costing companies time, money, and resources.
This article explores the best practices and essential tools to establish and maintain lubrication reliability, starting with a look at key principles, common errors, and the benefits of using professional tools like OilSafe products, available through providers like LubeworX.
Fundamental Principles of Lubrication Reliability
What is Lubrication Reliability?
Lubrication reliability is the assurance that machinery parts have the proper lubrication at the right time, preventing excessive wear, overheating, and eventual breakdown. Maintaining this reliability requires not just regular oiling but a holistic approach involving lubricant quality, the application process, and monitoring.
Key Factors Affecting Lubrication Reliability
To achieve reliable lubrication, certain factors must be addressed:
- Temperature and Pressure: Higher temperatures can thin oils, while extreme pressures can displace lubricants, requiring special formulations.
- Load and Speed: Heavier loads and faster speeds create more friction, impacting lubricant effectiveness.
- Contamination Control: Dust, debris, or moisture mixed with lubricants can lead to serious damage.
Types of Lubricants and Their Roles in Reliability
Mineral Oils vs. Synthetic Oils
Mineral oils are derived from petroleum and are commonly used in industrial applications due to their affordability. However, synthetic oils offer better stability under extreme conditions, though they are often more expensive.
Greases and Solid Lubricants
Greases are semi-solid lubricants ideal for components with higher load requirements. Solid lubricants, like graphite or molybdenum disulfide, are used where liquid lubricants may not be effective.
Lubrication Methods and Systems
Manual Lubrication Methods
Manual lubrication is a common approach, involving workers applying oils or greases to machinery. While simple, it’s prone to human error and inconsistency.
Automated Lubrication Systems
Automated systems deliver lubricants at regular intervals, improving reliability and reducing the chance of over or under-lubrication. Although they require initial investment, they provide consistent lubrication, improving machinery lifespan.
Best Practices for Effective Lubrication
Standard Lubrication Procedures
Developing a standard lubrication procedure can mitigate many common issues, ensuring that the right amount of lubricant reaches each part. Procedures should be tailored based on equipment requirements and should include step-by-step instructions for application, frequency, and amount.
The Six Lubrication Rights
Guide from selecting to implementing the Right type of oil
Importance of Cleanliness and Contamination Control
Cleanliness in lubrication can’t be overstated. Contaminated lubricants are a primary cause of machinery damage, so ensuring tools and storage areas remain clean is crucial.
Ideal Storage and Handling Practices
Lubricants should be stored in a cool, dry area away from contaminants. Handling tools must also be clean, and workers should be trained in proper handling techniques to maintain lubrication quality.
Bad Practices in Lubrication and Their Consequences
Visual Examples of Poor Lubrication Practices
Improper lubrication techniques, such as using an open oilcan to pour oil directly into machinery, lead to issues like over-lubrication, spillage, and contamination. These practices often cause premature machinery breakdowns.
Risks of Using Improper Tools for Lubrication
Using non-specialized tools like open oil cans introduces contamination and poses spillage risks. Additionally, without measurement control, it’s easy to add too much or too little lubricant, compromising reliability.
Best Practice Tools for Lubrication Reliability
Why Choose Professional Lubrication Tools?
Professional tools designed for lubrication not only ensure precise measurement but also protect lubricants from contamination. Tools like the OilSafe system reduce human error and simplify proper lubricant handling.
Overview of OilSafe Tools and Their Benefits
OilSafe offers a range of products from colour-coded oil cans to sealed pump systems that reduce contamination and increase accuracy. Their ergonomic design ensures safe and easy lubricant application, perfect for heavy-use industrial environments.
Recommended Best Practices with OilSafe Tools
Using OilSafe products alongside best practices, like regular inspection and proper storage, can significantly improve lubrication reliability. Available at LubeWorx, OilSafe’s products support companies in achieving lubrication goals efficiently.
Case Study: Poor Practice vs. Best Practice in Lubrication
Case Analysis: Open Oilcan vs. OilSafe Can + Pump
Imagine two scenarios: one where an operator uses an open oilcan to fill a machine, and another where they use an OilSafe can with a sealed pump system. The first practice risks contamination and inconsistent application, while the OilSafe can with a pump ensures an accurate and safe lubricant transfer, minimizing spillage and contamination.
The Long-Term Impact of Using the Right Tools
Over time, using proper tools can reduce the risk of machine failure, decrease maintenance costs, and increase operational productivity. This case study illustrates how small investments in high-quality tools pay off in the long term.
Maintenance Tips for Optimal Lubrication Reliability
Inspection and Condition Monitoring
Regularly inspecting lubrication points helps identify early signs of wear or contamination. Condition monitoring can be as simple as observing lubricant color and consistency.
Establishing a Routine Maintenance Schedule
A well-defined maintenance schedule prevents machinery failure. Regular checks, lubricant refills, and equipment adjustments reduce the likelihood of malfunctions.
Regular Lubricant Analysis and Quality Control
Analyzing lubricants regularly to check for contamination or degradation ensures the lubricant's effectiveness. Quality control also involves assessing storage conditions and replacing any contaminated stock.
FAQ Section on Lubrication Reliability
What is Lubrication Reliability, and why is it crucial?
Lubrication reliability ensures that machinery receives the right lubricant in the right amount, which is essential for smooth operation, reducing wear, and minimizing downtime.
How do OilSafe tools contribute to better lubrication practices?
OilSafe tools protect against contamination, provide accurate lubricant measurement, and ensure that lubricants are stored and applied effectively, all of which enhance reliability.
What are common signs of poor lubrication reliability?
Common signs include excessive noise, overheating, leakage, and visible wear or rust on machinery parts.
What happens if incorrect lubrication tools are used?
Using incorrect tools often leads to contamination, inconsistent lubrication, and the risk of under- or over-lubrication, all of which reduce machinery lifespan.
How often should lubricants be replaced or refilled?
It depends on equipment usage and environmental conditions, but most machinery should be checked and refilled every 1-3 months.
How does contamination affect lubrication reliability?
Contaminants like dirt, water, or other particles reduce lubricant effectiveness, increasing wear and the risk of breakdowns.
Conclusion: Building a Reliable Lubrication Strategy for Long-Term Success
Achieving lubrication reliability involves understanding proper methods, avoiding bad practices, and using high-quality tools like OilSafe products from LubeworX. By investing in the right products and implementing consistent procedures, companies can significantly improve equipment performance, reduce costs, and maintain uninterrupted production. With best practices and the right tools in place, businesses can build a long-term strategy for effective and reliable lubrication.