- 1. Lubrication Audits:
- 2. Lubrication Failure Analysis:
- 3. Lubricant Contamination Control:
- 4. Lubrication Monitoring:
- 5. Lubrication Reliability Metrics:
- 6. Lubrication Quality Control:
- 7. Lubrication Predictive Maintenance:
- 8. Lubrication System Design:
- 9. Lubricant Selection Criteria:
- 10. Lubrication Reliability Training:
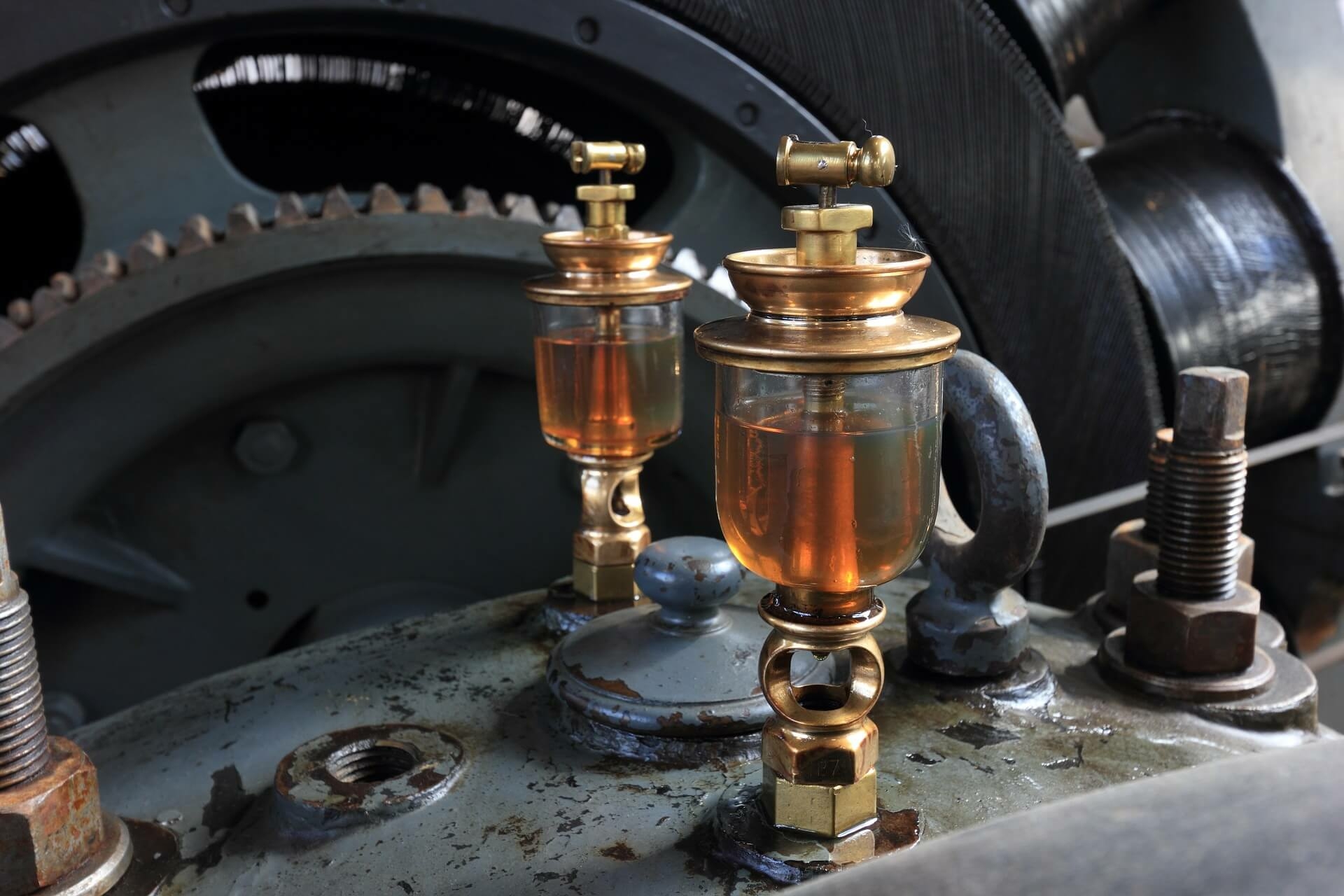
10 crucial points for achieving Lubrication Reliability
Determining the "best" points in Lubrication Reliability can vary depending on the specific needs and priorities of an organization. However, here are 10 key points that are generally considered crucial for achieving high lubrication reliability:
1. Lubrication Audits:
Lubrication Audits involve systematic assessments of lubrication practices and systems to identify areas for improvement.
Example: An external auditor reviews a manufacturing facility's lubrication processes, recommending changes to enhance reliability and reduce maintenance costs.
2. Lubrication Failure Analysis:
Lubrication Failure Analysis is the process of investigating and understanding the root causes and prevent recurrence.
Example: After a bearing failure, engineers conduct lubrication failure analysis to determine if the wrong lubricant was used or if contamination played a role.
3. Lubricant Contamination Control:
Lubricant Contamination Control refers to the set of practices and strategies employed to prevent, minimize, or manage the introduction of foreign particles, substances, or contaminants into lubricating oils or greases. Effective contamination control is critical for maintaining the quality and performance of lubricants and, by extension, the reliability and longevity of machinery and equipment.
Example:
Imagine a manufacturing facility with a hydraulic system that relies on hydraulic oil as a lubricant to operate various machinery. To ensure Lubricant Contamination Control, the facility implements several measures:
- Sealed Storage: The hydraulic oil is stored in sealed containers in a dedicated storage area with controlled temperature and humidity. This prevents moisture and airborne particles from entering the containers.
- Breathers and Desiccant Filters: The hydraulic reservoirs are equipped with breathers and desiccant filters. These devices help maintain a clean and dry environment inside the reservoirs, preventing the ingress of moisture and particulate contaminants.
- Filtration Systems: The hydraulic system includes high-efficiency filtration units that continuously filter the oil to remove particles and contaminants. This ensures that the oil circulating in the system remains clean.
- Regular Inspections: Maintenance technicians conduct routine inspections of the hydraulic system and lubricant reservoirs to check for any signs of contamination, such as visible particles or changes in oil color and consistency.
- Oil Analysis: Periodic oil analysis is performed to monitor the condition of the hydraulic oil. This includes tests for particle count, moisture content, and chemical composition. If contamination levels exceed acceptable limits, corrective actions are taken.
- Clean Transfer and Handling: When adding oil to the system or performing maintenance tasks, technicians follow strict procedures to ensure that the oil is transferred and handled in a clean and contamination-free manner.
By implementing these Lubricant Contamination Control measures, the facility maintains the quality of its hydraulic oil, preventing premature wear and damage to hydraulic components. This, in turn, helps ensure the reliability and efficiency of the machinery, minimizing downtime and maintenance costs.
4. Lubrication Monitoring:
Lubrication Monitoring involves continuous or periodic assessment of lubrication systems and equipment performance.
Example: Sensors are installed on critical bearings to monitor temperature and vibration, triggering alerts for potential lubrication issues.
5. Lubrication Reliability Metrics:
Lubrication Reliability Metrics are quantitative measures used to assess the effectiveness and performance of lubrication practices within an organization. These metrics provide insights into the reliability of lubrication processes and their impact on equipment health and maintenance efficiency. Here are some common Lubrication Reliability Metrics along with examples:
Mean Time Between Lubrication (MTBL):
Description: MTBL measures the average time interval between lubrication events for a specific piece of equipment.
Example: The MTBL for a critical pump is calculated as 60 days, indicating that, on average, lubrication is required every two months.
Lubrication Interval Adherence:
Description: This metric assesses the percentage of lubrication tasks performed within their scheduled intervals.
Example: If 90% of lubrication tasks were completed on schedule over a month, the Lubrication Interval Adherence for that period is 90%.
Lubricant Consumption Rate:
Description: Lubricant Consumption Rate quantifies the volume or weight of lubricant used per unit of time.
Example: A machine consumes 10 liters of oil per week, resulting in a Lubricant Consumption Rate of 10 liters/week.
Lubrication Cost per Operating Hour:
Description: This metric calculates the cost of lubrication activities per hour of equipment operation.
Example: If lubrication costs for a machine are $100 per week, and the machine operates for 40 hours a week, the Lubrication Cost per Operating Hour is $2.50.
Lubrication Task Completion Rate:
Description: It measures the percentage of lubrication tasks completed as planned within a defined timeframe.
Example: If 95 out of 100 scheduled lubrication tasks were completed within a month, the Lubrication Task Completion Rate is 95%.
Equipment Downtime Reduction:
Description: This metric quantifies the reduction in unplanned equipment downtime attributed to effective lubrication practices.
Example: Implementing a lubrication reliability program reduces downtime from 10 hours per month to 5 hours per month, resulting in a 50% reduction.
Lubricant Shelf Life Utilization:
Description: It measures the percentage of a lubricant's shelf life consumed before it is used.
Example: If a lubricant with a shelf life of two years is used within one year, the Lubricant Shelf Life Utilization is 50%.
Lubrication-Related Failures:
Description: The number of equipment failures directly attributed to lubrication issues.
Example: Over a year, there were 8 equipment failures caused by improper lubrication practices.
Oil Cleanliness Level:
Description: Oil Cleanliness Level assesses the concentration of particles in lubricating oil, typically measured as ISO cleanliness codes.
Example: An oil analysis report shows that the ISO cleanliness code for a hydraulic system's oil improved from 22/20/18 to 18/16/13.
Lubrication Audit Score:
Description: A score assigned to the results of lubrication audits, evaluating the adherence to best practices and standards.
Example: After a lubrication audit, the facility receives a score of 90 out of 100, indicating strong compliance with lubrication best practices.
These Lubrication Reliability Metrics help organizations track the performance of their lubrication programs, identify areas for improvement, and make data-driven decisions to enhance equipment reliability and reduce maintenance costs.
6. Lubrication Quality Control:
Lubrication Quality Control involves measures and processes to ensure lubricants meet specified quality standards.
Example: Lubricant suppliers perform quality control tests, including viscosity checks, to ensure product consistency.
7. Lubrication Predictive Maintenance:
Lubrication Predictive Maintenance is an approach that uses data analysis, condition monitoring, and predictive analytics to determine the optimal timing for lubrication-related maintenance tasks. By predicting when equipment will require lubrication, organizations can avoid over-lubrication or under-lubrication, leading to improved equipment reliability, reduced maintenance costs, and increased operational efficiency.
Example:
Let's consider a scenario in a manufacturing plant that utilizes a range of conveyor belts to transport materials throughout the facility. Proper lubrication of the bearings in these conveyor systems is essential for preventing premature wear and ensuring smooth operation. In the past, lubrication was performed on a fixed schedule, with maintenance technicians applying grease to the bearings every month.
With the implementation of Lubrication Predictive Maintenance, the plant takes the following steps:
Sensor Installation: Vibration sensors are installed on key conveyor belt bearings to monitor their condition continuously. These sensors measure vibration levels and temperature.
Data Collection: The vibration sensors collect data on bearing conditions and transmit it to a central monitoring system in real-time. This data includes vibration patterns, temperature variations, and operating hours.
Data Analysis: Using advanced analytics software, the plant's maintenance team analyzes the collected data. They establish baseline vibration and temperature profiles for healthy bearings.
Predictive Modeling: Predictive models are developed based on historical data and the baseline profiles. These models can predict when a bearing is likely to require lubrication based on deviations from the baseline.
Maintenance Alerts: The monitoring system is programmed to send maintenance alerts to technicians when a bearing's condition begins to deviate from the baseline. These alerts specify the optimal time for lubrication.
Scheduled Lubrication: Technicians receive alerts indicating that a particular conveyor belt's bearing needs lubrication. They schedule lubrication for that specific bearing, ensuring it is done at the right time, neither too early nor too late.
Ongoing Monitoring: The monitoring system continues to collect and analyze data from all sensors, allowing for continuous predictive maintenance of the conveyor belt bearings.
By implementing Lubrication Predictive Maintenance in this example, the manufacturing plant achieves several benefits:
Reduced Lubricant Usage: Lubrication is performed only when needed, reducing lubricant consumption.
Extended Bearing Life: Bearings receive timely lubrication, preventing wear and extending their lifespan.
Decreased Downtime: Predictive maintenance reduces unplanned downtime due to bearing failures.
Cost Savings: By optimizing lubrication practices, the plant reduces maintenance and lubricant costs while improving overall equipment reliability.
Lubrication Predictive Maintenance transforms lubrication from a fixed-schedule task into a data-driven, condition-based strategy that maximizes the efficiency and reliability of equipment maintenance.
8. Lubrication System Design:
Lubrication System Design involves planning and engineering lubrication delivery systems for machinery and equipment.
Example: Engineers design a centralized lubrication system for a manufacturing line, ensuring precise and consistent lubrication of critical components.
9. Lubricant Selection Criteria:
Lubricant Selection Criteria are a set of guidelines and considerations used to choose the most suitable lubricant for a specific application or piece of machinery. These criteria take into account various factors such as operating conditions, equipment type, and lubricant properties to ensure optimal lubrication performance and equipment reliability.
Example:
Let's consider the lubricant selection process for a large industrial gearbox used in a mining operation. The gearbox is responsible for driving a conveyor system that transports heavy loads of ore from the mine to the processing plant. Choosing the right lubricant for this critical application is essential for preventing premature wear and ensuring the gearbox's longevity. Here are some Lubricant Selection Criteria applied to this scenario:
Operating Temperature Range:
Criteria: The lubricant must operate effectively within the gearbox's temperature range, which can vary widely due to environmental conditions and heavy loads.
Example: The gearbox operates in an outdoor mining environment where temperatures can range from -20°C in winter to 40°C in summer. A lubricant with a wide temperature range is required.
Load-Bearing Capacity:
Criteria: The lubricant must have sufficient load-carrying capacity to handle the heavy loads and shock loads encountered in the gearbox.
Example: Given the substantial loads involved, a high-EP (extreme pressure) lubricant is chosen to protect against wear and scuffing under heavy load conditions.
Viscosity:
Criteria: The lubricant's viscosity should match the gearbox's requirements at various operating temperatures to ensure proper lubrication film thickness.
Example: The manufacturer's specifications recommend an ISO VG 320 viscosity grade for this gearbox under the anticipated operating conditions.
Water Resistance:
Criteria: Since the mining environment can be wet and dusty, the lubricant should have good water resistance properties to prevent water ingress and emulsification.
Example: A lubricant with water-repellent additives is selected to maintain its effectiveness in the presence of water and moisture.
Oxidation Resistance:
Criteria: The lubricant should resist oxidation and thermal degradation to maintain its performance over extended service intervals.
Example: An industrial synthetic gear oil with excellent oxidation resistance is chosen to ensure long service life.
Compatibility with Seals and Materials:
Criteria: The lubricant should be compatible with the gearbox's seals and materials to prevent seal degradation or material incompatibility.
Example: The lubricant selected is approved by the gearbox manufacturer and is known to be compatible with the seals and materials used in the gearbox.
Environmental Considerations:
Criteria: The mining operation has environmental regulations to follow, so the lubricant should meet environmental compliance requirements.
Example: The lubricant selected is biodegradable and meets environmental regulations, reducing the environmental impact in case of leakage.
Cost Considerations:
Criteria: While performance is critical, the lubricant selection should also consider cost-effectiveness and budget constraints.
Example: After evaluating various lubricants, a cost-effective option meeting all performance criteria is chosen to optimize total cost of ownership.
By applying these Lubricant Selection Criteria, the mining operation ensures that the chosen lubricant is the best fit for the gearbox's specific requirements, minimizing maintenance issues, maximizing equipment reliability, and adhering to environmental standards.
10. Lubrication Reliability Training:
Lubrication Reliability Training is an essential component of any maintenance and reliability program aimed at optimizing lubrication practices within an organization. This type of training provides personnel with the knowledge, skills, and expertise needed to ensure that lubrication processes are carried out effectively, efficiently, and in a manner that promotes equipment reliability and longevity.
Here are some key aspects of Lubrication Reliability Training:
Lubrication Fundamentals: Training typically starts with the basics, covering the science of lubrication, lubricant properties, and the importance of proper lubrication in machinery.
Lubricant Selection: Participants learn how to select the right lubricants for specific applications based on equipment requirements, operating conditions, and compatibility.
Lubrication Techniques: Training includes hands-on instruction in lubrication techniques, such as oil and grease application, to ensure proper methods are followed.
Contamination Control: Participants learn how to prevent and manage lubricant contamination to maintain the cleanliness of lubricants and equipment.
Lubrication Equipment: Training may cover the proper use and maintenance of lubrication equipment, such as pumps, dispensers, and lubrication delivery systems.
Oil Analysis: Understanding oil analysis techniques and interpreting oil analysis reports is a crucial part of Lubrication Reliability Training.
Predictive Maintenance: Training often includes predictive maintenance concepts related to lubrication, such as condition monitoring and data analysis.
Safety Protocols: Participants are educated on safety protocols for handling lubricants, including the use of personal protective equipment (PPE) and safe disposal practices.
Documentation: Training emphasizes the importance of accurate record-keeping and documentation of lubrication activities, including lubrication schedules and equipment history.
Troubleshooting: Participants learn how to troubleshoot lubrication-related problems and perform root cause analysis for lubrication failures.
Regulatory Compliance: Training covers relevant industry regulations and standards related to lubrication practices, ensuring compliance with legal requirements.
Continuous Improvement: Lubrication Reliability Training often emphasizes the importance of continuous improvement, encouraging personnel to seek ways to optimize lubrication practices continually.
Certification Programs: Some organizations offer certification programs in Lubrication Reliability, allowing individuals to demonstrate their expertise in lubrication practices.
Customized Training: Training programs can be customized to suit the specific needs and challenges of an organization's equipment and industry.
Ongoing Education: Lubrication technology evolves, and ongoing education is essential to keep personnel up-to-date with the latest advancements and best practices.
Lubrication Reliability Training helps organizations achieve a high level of competence in lubrication practices, resulting in reduced maintenance costs, improved equipment reliability, and increased overall operational efficiency. It empowers personnel with the knowledge and skills needed to make informed decisions and maintain equipment at peak performance.
These points lay the foundation for a robust lubrication reliability program, helping organizations achieve efficient equipment operation, extended machinery life, and reduced maintenance costs.