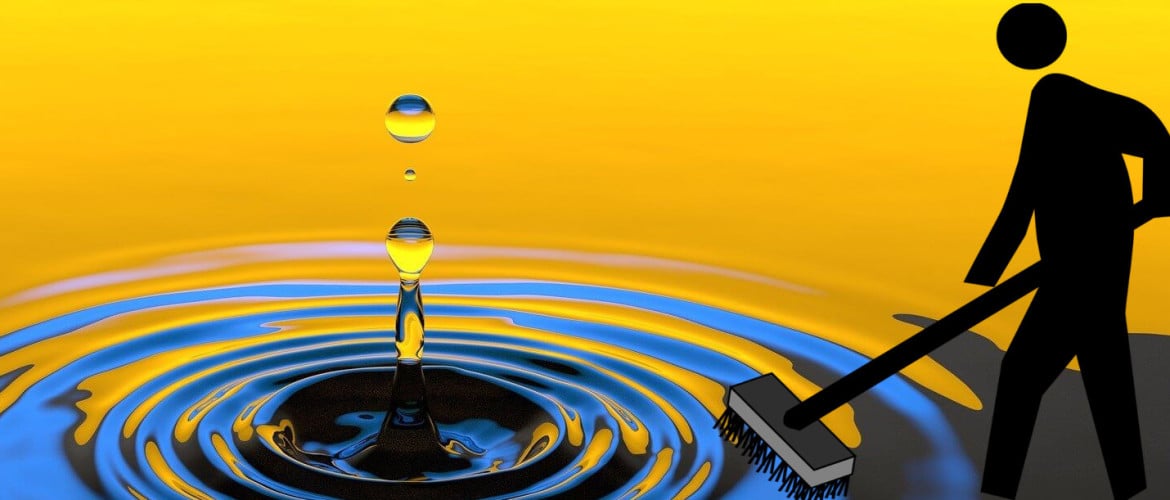
ISO 4406 - the cleanliness code explained
ISO 4406 - the cleanliness code explained
The number one problem with lubrication today is contamination, and this can be particle contamination or chemical contamination or both. A Lubrication Reliability strategy consistently uses three words:
- Cleanliness,
- Contamination and
- Control,
and when combined they are generally used as cleanliness control and contamination control.
Cleanliness and Contamination Control
Cleanliness control is the processes and tools to ensure only clean lubricants are added to the equipment, whereas Contamination Control is the processes and tools to ensure only clean lubricants are operating in the equipment
Contamination is the major cause of failure in fluid power systems. That's why a very valid and important question is: "How do we get and maintain an acceptable fluid cleanliness level?".
The International Organization for Standardization (ISO) created the cleanliness code ISO 4406 to quantify particulate contamination levels per milliliter of fluid at three sizes. The particle sizes range from tiny little chunks to big, irregular shapes, and were grouped into 4 micron, 6 micron and 14 micron sizes. It is this code that is used by most companies to set their targets for lubrication cleanliness.
So, apart from:
- the standardised method of measuring and describing the cleanliness of the fluid, it also created:
- guidelines for determining how clean the fluid should be for a given system.
Now having the tool to measure, one should not forget that samples should be drawn in the right way and in the right location. Sampling should always be taken when oil moves through the system. Otherwise it will not give an accurate picture of what is happening inside the machine.
What do the ISO numbers mean?
The ISO code is expressed in 3 numbers, for example 22/18/13 (see example below). Each number represents a contaminant level code for the correlating particle size. Let's go through the list step by step:
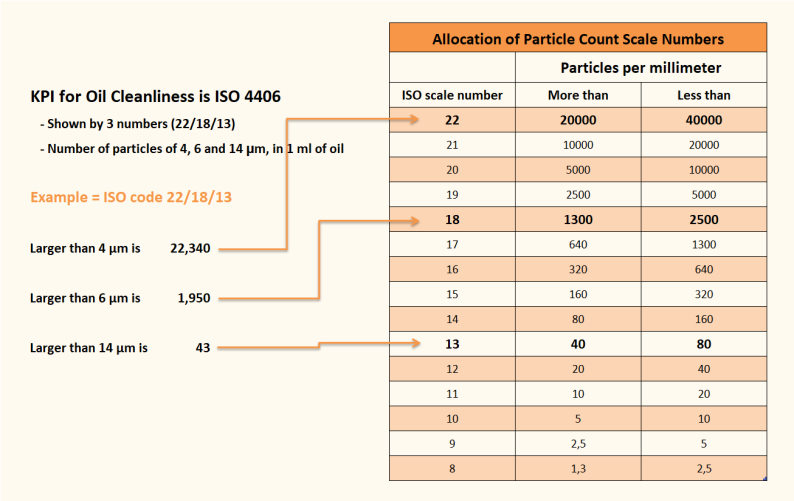
1. Size of the particle
There are 3 size groups:
- size ≥ 4 -
- size ≥ 6 -
- size ≥ 14µm
2.The sequence of the ISO number and its meaning (example 22/18/13 )
- The 1st number (22) represents the range of particles that are 4µm or larger in 1 ml (1 cc)
- The 2nd number (18) represents the range of particles that are 6µm or larger in 1 ml (1 cc)
- The 3rd number (13) represents the range of particles that are 14µm or larger in 1 ml (1 cc)
Note: the first number is never smaller than the second number. The second number is never smaller than the third number.
3. Particles counted/reported
The particles are counted in a sample of 100 ml, but reported in 1 ml
Particles reported
The number 13 does not mean that there are 80 particles counted. It means that somewhere between 40 (12) and 80 (13) particles are counted. What is reported is always the maximum contamination level. In this case 13.
4. The squared numbers
In fact not the actual particle count is given, but it describes how it relates to the factor of 2 (column 3). Eg. if there were 64 particles count in 100 ml there would be 2 x 2 x 2 x 2 x 2 x 2 = 26 number of particles. Then we will get the number 6 as the count.
5. Explanation of the numbers
- 22 means: we can expect to find between 20000 and 40000 particles size >4µm in 1 ml fluid
- 18 means: we can expect to find between 1300 and 2500 particles size >6µm in 1 ml fluid
- 13 means: we can expect to find between 40 and 80 particles size >14µm in 1 ml fluid
Target Cleanliness Levels
Companies that are managing their lubrication contamination have ISO 4406 targets for different applications and set targets accordingly, depending on the criticality of the machine in their processes. Below are some examples of recommended target levels.
- Hydraulics 15/13/10
- Turbines 16/14/11
- Engines 17/15/12
- Gearboxes 18/16/13
Conclusion
Lubrication practices within a plant have a direct effect on plant and equipment reliability. When the lubrication is working effectively, wear will be reduced and equipment reliability will be improved. A Lubrication Reliability strategy focuses on all parameters that protect the average lubrication film thickness thereby reducing component wear and increasing equipment reliability.
How important it is to reduce contamination and to keep your components and machines clean, is clearly shown below in Caterpillar's video: Fluid Contamination | "The Silent Thief".